国企蜕变的“兰溪故事”: “脱胎换骨”勾勒改革新路径
中新网金华3月11日电(记者 奚金燕)站在中国经济行至由大变强的十字路口,作为国民经济基础的国企经济如何转型升级,堪称关键。
当下,各地实践已全面开启。其中,国企蜕变的“兰溪故事”颇为引人注意。诞生于计划经济时代的浙江省华东铝业股份有限公司,曾是华东地区最大的有色金属冶炼加工企业之一。而随着电力成本的上升,华铝陷入亏损。
面对生死存亡,华铝选择毅然淘汰落后产能,腾出空间,引入光学膜生产项目,走向重生。在这里,华铝通过一场“脱胎换骨式”的革命,演绎新常态下传统经济的创新活力,为国企改革提供了一个可借鉴范本。
计划时代骄子?工业经济独领风骚
纵观兰溪工业版图,传统龙头企业——华铝,是一个引人注目的坐标。
华铝,前身是兰溪铝厂,始建于1958年5月,由前苏联援建,曾是华东地区最大的有色金属冶炼加工企业之一。
上世纪末,市场经济蓬勃发展,国有经济渐显疲态。1994年初,当时的兰溪市委积极在国有企业中推进产权制度改革,大力推行股份制和股份合作制,建立现代企业制度,由此拉开国有企业改制的序幕。
华铝紧抓这一轮改革机遇,股权几番变更,最终更名成了华东铝业。从2000年至2013年,华铝生产规模翻了近五倍,年销售额从8亿元增长为47亿元,累计实现销售额336亿元,利润7.88亿元,堪称兰溪工业的一面旗帜。
然而将日历翻到21世纪,随着国家对电解铝等高耗能行业出台了一系列调控措施,华铝渐渐感觉到了“压力山大”。
“电解铝主要靠电,刚建起来的时候,电就三分多一度,可到了2011年要6毛一度,要知道电价每提高一分钱,我们的成本就要多两千万。”华铝副总经理李炜明苦笑着说。
为求生存,从2009年开始,华铝率先在国内应用“新型阴极电解槽技术”,将铝液交流电耗控制在了13201千瓦时/吨,比行业平均水平要低700-1000千瓦时/吨。
然而好景不长,由于铝的价格逐年走低,电的成本逐年提高,最后还是出现了成本倒挂的情况,陷入亏损。
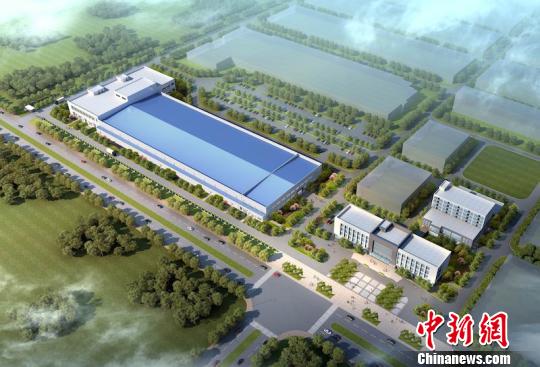
渐渐褪去光环?困境之中寻求突围
2012年,华铝全年用电量为21亿千瓦时,超过武义县全社会工业用电量(15.06亿千瓦时),是磐安县的7.1倍……显然,在浙江这样的电力资源小省,继续发展电解铝行业是无以为继的。
浙江省委、省政府曾旗帜鲜明提出,实体经济是浙江发展之基,困境中更要坚守。对华铝而言,要坚守惟一的选择就是“脱胎换骨”式改造。
在金华市政府和兰溪市政府的推动下,2013年7月29日,华东铝业由杭州锦江集团、红狮控股集团顺利完成战略重组。2014年,华东铝业彻底关停了高耗能的电解铝生产线。
“归零”之后的华铝将目光瞄向了高技术、高附加值的光学膜新材料产业。
“兰溪工业有基础有体量,但附加值不高,振兴兰溪工业绝不能走老路。”在兰溪市主政者看来,兰溪传统工业要转型升级必须要引进分量重、成色足、含金量高的大项目,通过一个项目带动一个产业,甚至推动整个城市的转型升级。
经过一段时间的接触,最终,光学膜产业园花落兰溪。光学膜产业园项目由杭州锦江集团引进,华铝主体实施,计划投资30亿元,占地面积1000亩。
“台湾有技术有设备,我们有人才有市场,双方可以说是强强联合。”李炜明说道。
积极转型升级?脱胎换骨再造优势
光电信息产业中最具发展前景的通讯、显示和存储三大类产品都离不开光学薄膜,它的性能在很大程度上决定了这些产品的最终性能。由于技术原因,目前仍大量依赖进口。
记者了解到,目前,华铝光学膜产业园已落户的两个项目,分别是浙江锦辉光电材料有限公司实施的年产7200万平方米液晶屏背光模组增亮膜项目和浙江锦宏新材料科技有限公司实施的年产3600万平方米TFT偏光增亮膜项目,全部投产后预计实现年销售收入35亿元。
目前,第一批液晶屏背光模组增亮膜产品正在下线,产品比一张A4打印纸还要薄,非常光亮,又很柔和。
“这张膜是运用超精密加工技术,它的线宽可以做到5个微米,雕刻机台精度可以达到1个微米,还运用超精密的光学技术,让整个增亮膜的增亮效果可以超过60%。”据锦辉光电制造中心总监苏文卫介绍,小到手机、数码相机的屏幕,大到笔记本和平板电脑,甚至超大彩电屏幕都需要使用增亮膜,市场前景广。
根据锦江集团光学膜产业链整合的规划,下一步还将不断引进相关项目落户产业园,带动上下游发展,形成产业集聚,逐步将产业园打造成一流的光学膜制造与研发示范基地。
一子落期满盘活。以光学膜产业园为发展载体,兰溪正在规划建设一个层次高、结构紧、创新强的光膜特色小镇,实现兰溪产业转型提升。
“即使现在面临着阵痛,但我们依然要咬定目标走下去,重新恢复兰溪工业的辉煌。”正如兰溪市委书记朱瑞俊所言,兰溪工业转型升级任重而道远。(完)